Hypersonic flight, near or greater than Mach5 and below altitudes of around 90 km, has been the subject of decades of military research. Critical to national defense, the technology presents any number of challenging hurdles and complications. At a fixed altitude within the stratosphere, the faster a vehicle travels the more air resistance it faces. More thrust and fuel is required and, as the air compresses, aerodynamic drag and vehicle skin temperature increase.
In recent years, hypersonic missiles and other hypersonic weapons have started to
come into play. In May 2022, the Russians became responsible for the first combat use of a hypersonic maneuvering missile—a weapon of speed, unpredictability, and altitude—when they launched three missiles at the Ukraine port city of Odesa, leveling hotels and a shopping mall. This event, while not surprising, has only solidified the urgency for the United States to have both offensive and defensive hypersonic programs.
As hypersonic technology has developed, one of the problems has been how to accurately test and evaluate it, with ground infrastructure, in order to reduce failures and shortfalls even while saving time and resources during the development process. In recent years, CFD Research Corporation has been working with the Department of Defense through the Small Business Innovative Research (SBIR) program to upgrade ground test infrastructure capable of measuring hypersonic vehicle system/ component performance and durability under a multitude of different flow parameters and conditions, even while accounting for test article size and run duration.
Based in Huntsville, Alabama, CFD Research executes both fundamental and applied hypersonic technology research and development through the SBIR program. Their signature simulation software has evolved over decades, and has incorporated a multitude of fundamental physics and chemistry-based modeling techniques capable of simulating and addressing complex hypersonic flow phenomena within a hypersonic flight environment.
Still, there remains no single ground test infrastructure that can duplicate all the conditions and parameters within a hypersonic flight environment. Arnold Engineering Development Complex (AEDC)—an Air Force Material Command facility located in Tullahoma, Tennessee—operates aerodynamic and propulsion wind tunnels to ground test and evaluate aircraft, missile, and space systems. At Arnold Air Force Base, Tunnel B can achieve air flow speeds approaching Mach 8. Tunnel C can generate Mach numbers between 8 and 10, depending upon nozzle configuration. AEDC’s hypervelocity wind tunnel in White Oak, Maryland, features nozzles that provide Mach numbers of 6.7, 8, 10, 14, and 18. These different nozzles offer investigators the opportunity to investigate vehicle behaviors and performance across a broad range of Mach numbers and associated mission trajectories. CFD Research continues to work with AEDC to upgrade a variety of ground test infrastructures focused on mimicking specific hypersonic flight environments.
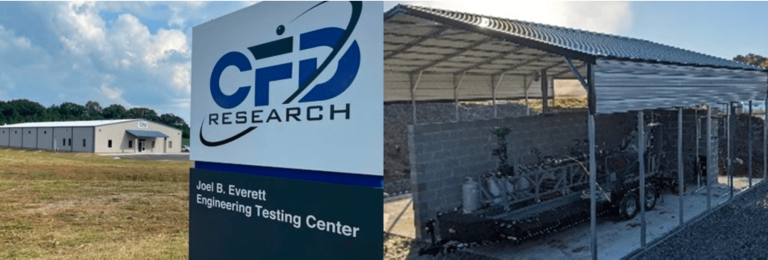
One wind tunnel, in particular, is an example of how an SBIR contract can make a big difference in hypersonic infrastructure test operations. AEDC’s Aerodynamic and Propulsion Test Unit (APTU), is a blow-down wind tunnel that serves as the largest available ground-based hypersonic system flight test environment in America today. It was built in 1981 and was upgraded in several phases between 2002 and 2008. Despite several upgrades multiple unstable combustion air heating behavior issues remained. CFD Research responded to SBIR Phase I Topic AF141-230 that targeted the need for a laser ignition system focused on mitigating the APTU combustion air heater startup instability behavior.
Upon selection and award of this SBIR contract, CFD Research identified that a more fundamental problem existed within the APTU combustion air heater that a laser-based ignition system could not resolve. Matt Thomas, the Principal Investigator of the SBIR Phase I effort, communicated to the Air Force that a laser ignition system was not going to resolve the unique flame propagation and stabilization issues. The tech company needed to convince the Air Force that a completely different approach to enhancing APTU combustion air heater operation necessitated a complete pivot from the original SBIR Phase I objectives.
“This was initially controversial,” Thomas said. “But we convinced the Air Force to support our recommendations and change the scope and direction of the SBIR Phase II project. Ultimately, we were able to fully resolve the propagation and stabilization problems and optimize APTU combustion air heater operation throughout its required performance envelope that included important startup and shutdown protocols.
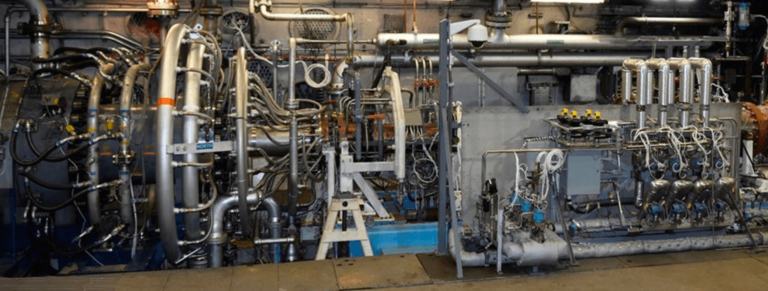
During Phase II a single injector was optimized in a customized test infrastructure and subsequently configured within a 37-injector arrangement tailored for installation within the APTU combustion air heater system assembly at the CFD Research Joel Everett Engineering Test Center.
The Air Force installed and utilized this injection system to complete multiple direct-connect scramjet (scramjets are supersonic combustion ramjets—a variant of ramjet jet engines) test programs as well as executed multiple test events within an APTU free jet test environment.
This APTU combustion air heater upgrade has already contributed significantly to the United States’ ability to ground test hypersonic vehicles and engines at realistic operating conditions.
A successful hypersonic test was documented in an August 2019 article posted as a news item on the Wright Patterson AFB website: “AFRL achieves record-setting hypersonic ground test milestone. The article mentions that “the AEDC team also successfully leveraged technology developed by CFD Research Corporation under the Small Business Innovative Research pro- gram. This technology proved crucial in achieving most of the required test conditions.”
During a follow-on project sponsored through the USAF SBIR Commercialization Readiness Program CRP), CFD Research developed, manufactured, and delivered to the USAF several sets of fuel injectors optimized for installation and operation at APTU test section, numbers ranging from Mach 3 to Mach 8. This SBIR CRP program was completed in August 2022. All of these SBIR contracts have provided a major return on investment while revitalizing an aging American hypersonic infrastructure test asset that would have required hundreds of millions to replace, even while permitting immediate test and evaluation of hypersonic technologies and concepts.
“And now CFD Research is scheduled to receive additional sponsorship focused on extending APTU run time from three minutes to fifteen minutes thereby enabling ground test and evaluation over an entire mission,” Thomas said.
APTU infrastructure supersonic and hypersonic system test customers include Army, Navy, and Air Force organizations; MDA, NASA, private industry, allied foreign governments and educational institutions. “We’ve encountered numerous challenges along the way that we’ve been able to overcome thanks to the dedication and creativity of the team,” Smith said. “We’ve learned quite a bit, and I’m proud of what we’ve accomplished. These groundbreaking tests will lead the way for future hypersonic vehicles for a range of missions.”
Article pulled from Defense SBIR/STTR Program Quarterly Review – Q1 Volume 2, Issue 1. Download the full newsletter by clicking here.